
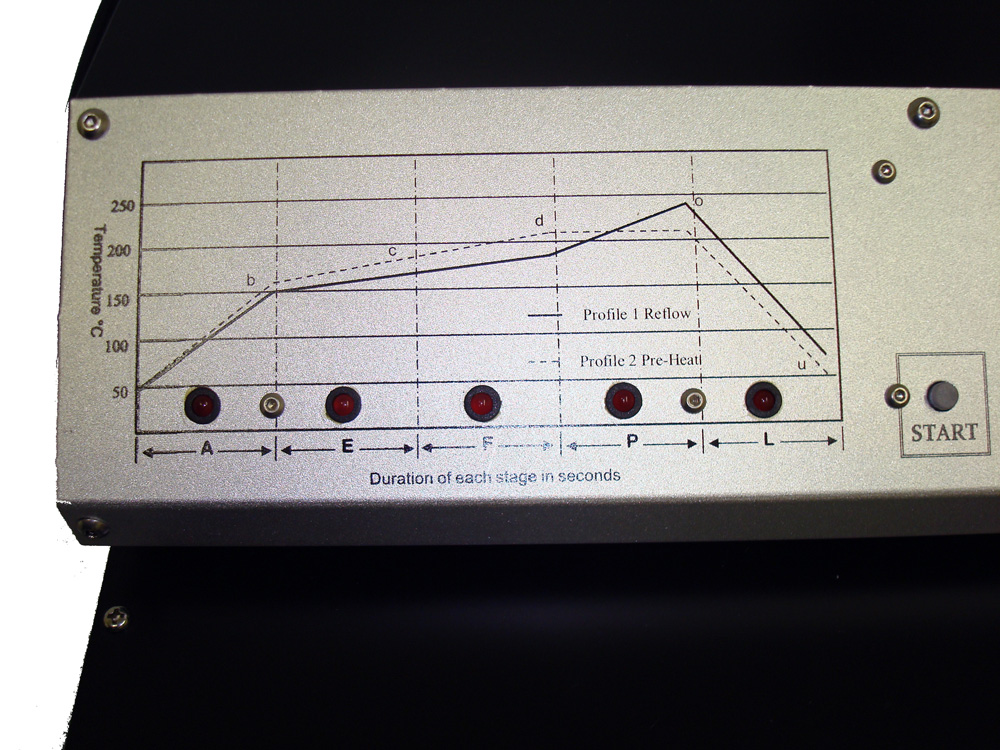
This ensures that the molten solder can wet the welding surface well. Another important role of this stage is that the flux in the solder paste begins to react actively thereby increasing the wettability (and surface energy) of the welding surface. This helps to reduce the thermal stress impact in the reflow zone and limits other soldering defects such as component lifts at larger volumes. The first is to achieve a uniform temperature for the entire PCB board. The setting of the constant temperature zone is mainly controlled within the parameters of the solder paste supplier and the heat capacity of the PCB. This is especially true for solder pastes with a high flux content. Another side effect of too high of a heating rate is that the solder paste can collapse and cause a short circuit. Too high of a heating rate will cause thermal stress on the components that can damage the component or reduce the performance/lifespan of the components. The preheating zone needs to volatilize the solvent but it must control the rising temperature. The role of the solvent is mainly as a carrier for the resin with the additional function of ensuring sufficient storage time of the solder paste. The main components of flux in the solder paste include resin, active agent, viscosity enhancer and solvent. The purpose of the preheating zone is to volatilize the lower melting solvent in the solder paste. These steps are meant to precisely control the melting and cooling of the solder to fill in the solder joints. The main temperature changes associated with the reflow soldering temperature curve can be divided into four phases/zones (listed below and pictured thereafter) : On a double-track conveyor belt, the boards with newly-placed components are passed through hot and cool zones of the reflow furnace. (To learn the Basics of SMT Reflow Temperature Plate click here) The parameters of certain components will also directly impact the temperature curve selected for this step in the process. The temperature curve associated with the reflow is an essential parameter to control to ensure the correct connection of parts. Reflow soldering is an extremely vital step in the SMT(Surface Mount Technology) process.
